How Zenni and OSARO Automated Eyewear Fulfillment with Robotics
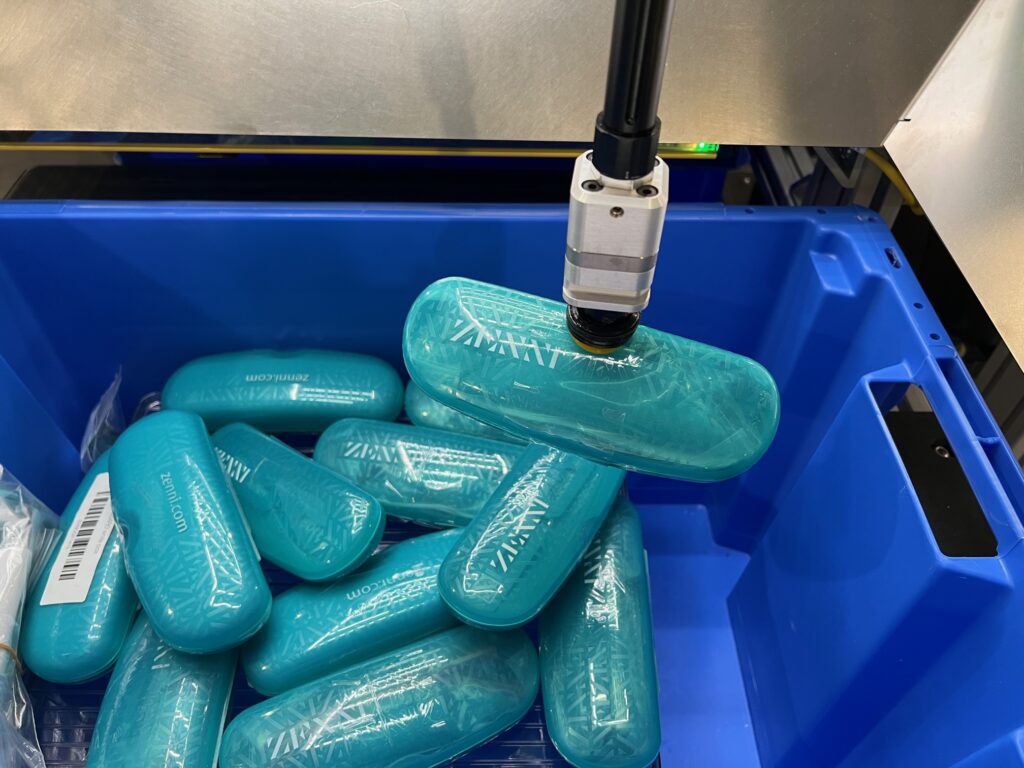
80% INCREASE IN THROUGHPUT
99.9% ACCURACY
UP TO 410 UNITS/HOUR

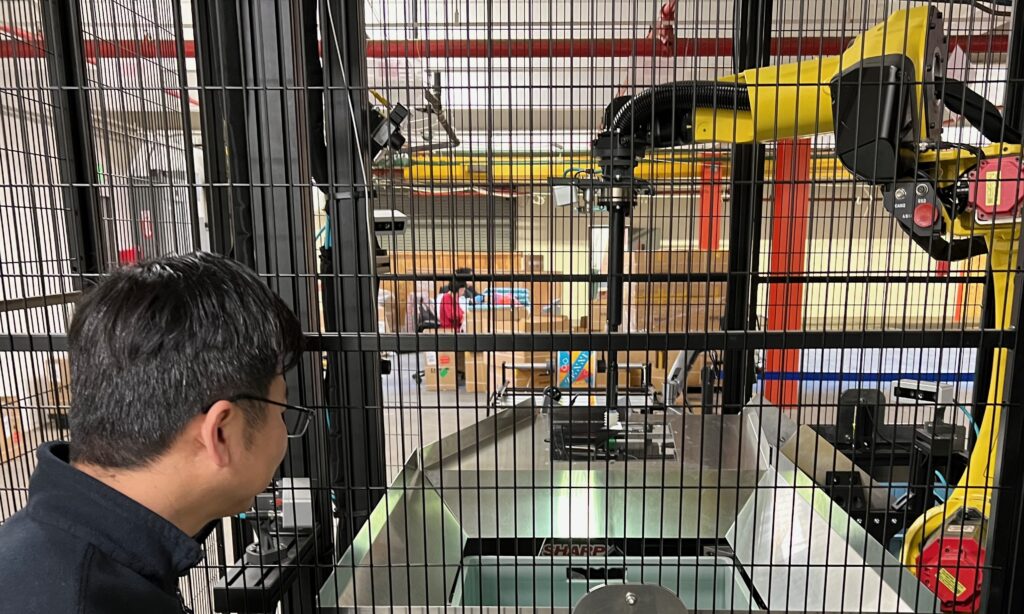
Robots and People
Leveling the Playing Field
By OSARO Staff
When robots entered the warehouse, Zenni Optical’s automation champion Simon Goh made a stunning discovery about worker productivity. The robots made his workers more productive – way more productive.
Goh knew that people worked at varying levels, but he didn’t realize what a difference robotics could make in the fulfillment process. In one audit comparing worker output on a manual station versus working with a robot over five-day periods, he discovered that the robots made his slowest workers up to 70% more productive. And even his fastest manual processor’s performance shot up 20%.
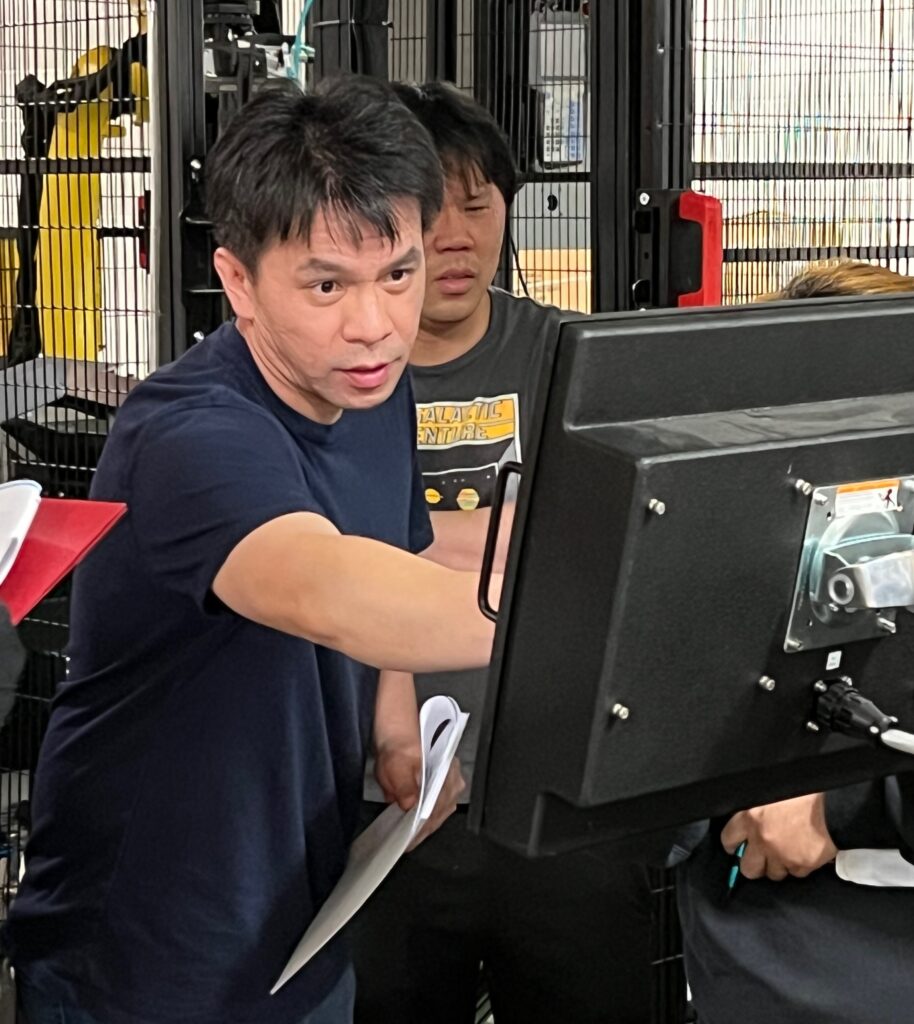
The metrics Goh collected over several months varied, but the upward trajectory was consistent. “With robots we have leveled the playing field for our employees, he said. “Now their performance is more even. It reduces mistakes and increases productivity.”
The increase was not only due to fast, consistent throughput by the robot. By employing robotics, the company was able to cut the number of steps needed to process a pair of eyeglasses for shipping from five steps to two steps, making everyone more productive.
Moreover, it took fewer people to process the products and employees could be assigned to other more interesting tasks that still require human intervention.
Workers seem to like it, too. Their work is streamlined, more varied, and they have acquired new skills. “Managing the robot is easier and better than stuffing packages,” said Minjie Hu, who has just completed training as a robot operator. “Learning new skills is better.” Adds Shipping Supervisor Blyn Prokopowich, who oversees the processors, “Robots have removed tedious tasks and enable us to deploy our team to do other projects like returns and multiple orders.”
Contrary to media hand wringing about robots taking people’s jobs, Goh says Zenni has no plans to lay off anyone. “Automation is going to help retain jobs in the U.S.,” he said. “The U.S. has higher labor costs, but with robots you can reduce the difference between the U.S. and developing countries.”
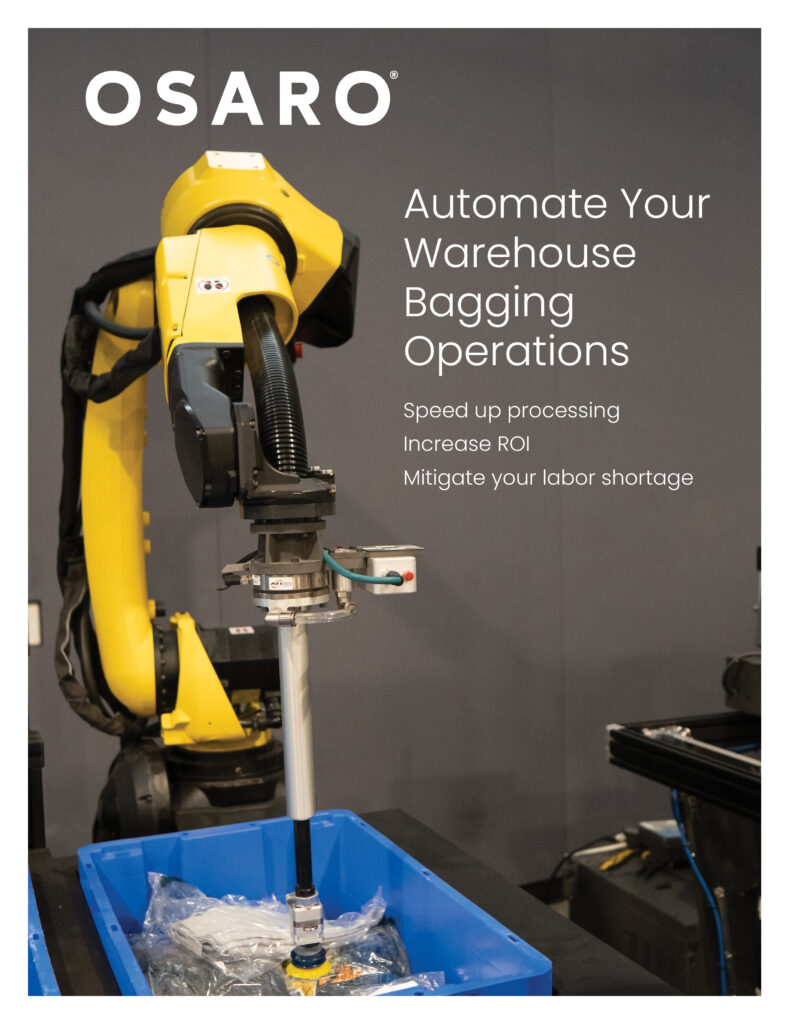
Learn more about how automated bagging can benefit your warehouse.
By OSARO Staff | OSARO Insights | Ask an Expert series
Wearing spectacles is no longer a tribulation reserved for the nearsighted or the bookworm. In recent years, as prices have come down, eyeglasses have become as much a fashion statement as a necessity. And no one knows that better than California-based Zenni Optical, one of the top 4 online eyeglass retailers. Zenni sells a whopping 6.5 million pairs annually – 6 million of them in the U.S. market alone.
Now in its 20th year, the first online-only eyewear retailer has surpassed 50 million pairs of glasses sold, and has doubled sales in just the last four years. “We offer quality eyewear at an affordable price,” says Simon Goh, Zenni’s Director of Distribution and Facilities. The crush of orders has made automation an imperative.
Automation pioneer
Zenni not only pioneered online eyewear, it also experimented early with automation. The company ships about 3 million eyeglasses to its U.S. customers annually from a modest warehouse tucked away in the bucolic hamlet of Novato, 28 miles north of San Francisco. Another 3 million ship from an Ohio facility to East Coast customers.
For years, workers hand scanned the barcoded eyewear, placed them into clamshell glass cases, and then inserted the cases into a tabletop mechanical bagging machine which spit them out in a labeled poly bag for shipping. The multi-step process was mind-numbingly tedious, slow, and prone to error. If just one item scanned out of sync with the product, it could result in unhappy customers squinting through incorrect lenses, returns, costly replacement product, and a loss of invaluable customer trust.
Goh, with encouragement from the company’s founder, started to innovate the process nine years ago. At first, progress automating the tabletop routine was incremental because the technology just wasn’t there, he said. They had started by introducing the hand scanners, then a centralized address and label system, and later, the tabletop packaging machine. Then, two years ago, Goh began investigating the newest generation of artificially intelligent industrial robots, visiting trade shows and learning the industry.
In 2022, he put his faith in OSARO’s machine learning-enabled robot using SightWorks™ vision and control software. “We thought that the technology is finally in place and at an affordable cost to the operation,” said Goh. “OSARO integrated everything together to provide a workable solution for our automation.”
The deployment of three OSARO® Robotic Bagging Systems was in full swing at the Novato facility in spring, 2023.
Up to 410 eyeglasses an hour
By June, each robot was able to pick, scan, bag, and label up to 410 eyeglasses an hour, an increase in throughput of 80%, according to Goh. The average can hover closer to 350 an hour when downtime to replenish bags or maintain the system is considered, but the system’s machine learning is also expected to continuously improve performance over time.
Goh estimated that two people working with the robots in a new process that reduced handling from five steps to two steps could do the work that previously required three people – faster and more accurately. He estimated a 50% increase in productivity.
With seasonal surges sometimes creating a need to suddenly process many more units in a single month, robots provide valuable processing flexibility. They can work longer than humans, allowing the company to redeploy people to other tasks that still require human intervention, such as unpacking boxes or processing returns.
Not just speed but accuracy
Zenni’s goals included not only achieving productivity gains but boosting accuracy – the coin of the realm for a product as personal as prescription lenses. If a customer receives the wrong pair of glasses, its brand integrity is damaged and trust is hard to recover.
By moving to a new process with robotics, Zenni was able to achieve 99.9% accuracy by reducing most of the risks inherent in manual processing. Errors were reduced from 20 per 100,000 to less than three per 100,000.
An ecosystem of partners
Eyeglasses, which are manually placed in translucent blue Zenni-branded cases, are brought in large bins to the robots. In each of the three integrated robotic system cells, the robot picks the eyeglass case and waves it in front of a scanner that reads the barcode unique to each pair through the case. Then, the automated bagging machine prints the address matching the barcode on a poly bag as the robot drops the case into a funnel on the bagger, where the item is sealed in the bag, and spit out onto a conveyor bound for shipping.
While OSARO’s SightWorks™ delivers the intelligence needed to precisely and delicately grasp, pick up, and place the eyewear into a poly bag, the company has lined up partners from which it can draw to meet a given customer’s needs. “We’ve developed the OSARO Partners Alliance, which is an ecosystem of the best technologies and vendors that we have found in the industry,” said VP of Operations Gemma Ross, who oversees manufacturing, customer success, field operations, and technical support at OSARO. “We have brought all of these together into our solutions to deliver the best for our customers.”
“Before we engaged with OSARO, we thought of doing some kind of robotic automation ourselves. Looking back, I can’t imagine we would have even considered that. We have to integrate so many different pieces of equipment; it’s just impossible to do without a professional company like OSARO.”
Simon Goh, Director of Distribution and Facilities
The key components of the OSARO® Robotic Bagging System are a FANUC M-10 Series robot powered by OSARO’s advanced vision and control software, a Pregis Sharp automated bagging machine, Cognex DataMan scanners, Framos cameras to guide the robot, and Smart Vision lighting.
The Framos cameras send information to the robot which stores the positions, dimensions and experience of each grasp pose to inform and improve its future picks. SightWorks™ effectively allows the robot to learn and get smarter as it gains more experience with similar items, and in other use cases, with many different SKUs.
Challenges
Partner vendors solved important challenges particular to Zenni. The eyewear maker’s signature glass cases stymied several scanner-makers that had difficulty reading barcodes through the translucent blue plastic case. OSARO sought and vetted a number of suppliers before landing on Cognex’s DataMan that outperformed others and was easy to use in the field.
Similarly, OSARO’s deployment support team worked with vendors to troubleshoot other problems. For example, printer lines or wrinkles in the shipping labels sometimes made it impossible for postal services to track the item during shipping – a reassurance customers have come to expect as they are notified of their purchases in transit. OSARO worked with Pregis to install a barcode verifier so that an alert would sound any time a printed label coming out of the bagger was not trackable. The item could be identified and properly reprocessed. The alarms to alert operators to tracking problems reduced untrackable items to nearly nil.
Results
Within several weeks of full deployment, OSARO’s robots had processed more than 100,000 pairs of eyeglasses. Working together, OSARO’s dedicated on-site customer deployment director and the Zenni team met challenges such as integrating database communication between the new robotic system and Zenni’s proprietary order-intake software, procuring necessary parts amidst supply chain disruption, and solving vendor coordination issues, as well as the prickly barcode scanning problem. “I was pretty skeptical and worried at the beginning,” said Goh. “But the end result has been good. We don’t have to talk about scanning at all at our daily meetings anymore.”
End-to-end customer support
Considering the automation journey from start to finish, Goh said he couldn’t have done it without OSARO’s constant intervention and vigilance, a process OSARO calls its Hypercare customer support program. “Before we engaged with OSARO, we thought of doing some kind of robotic automation ourselves,” said Goh. “Looking back, I can’t imagine we would have even considered doing that. We have to integrate so many different pieces of equipment; it’s just impossible to do without a professional company like OSARO.”
For OSARO, its advanced AI-driven technology enables the intelligent robotics that makes the project work, but it is just one part of the engagement. “Our Hypercare customer support program was purposefully designed to tackle the inevitable complexities of implementing a new fulfillment process,” said Ross. The five-phase program included: Scoping, Installation, Acceptance, Deployment, and Performance Monitoring.
“We went through all the issues we needed to deal with every week. We were working together more like a partner, trying to address each issue,” said Goh, who warns it can go in either direction. Without full vendor support, a project can go haywire. “OSARO’s approach with the end-to-end solution is actually the easiest way for anyone who wants to do automation.”
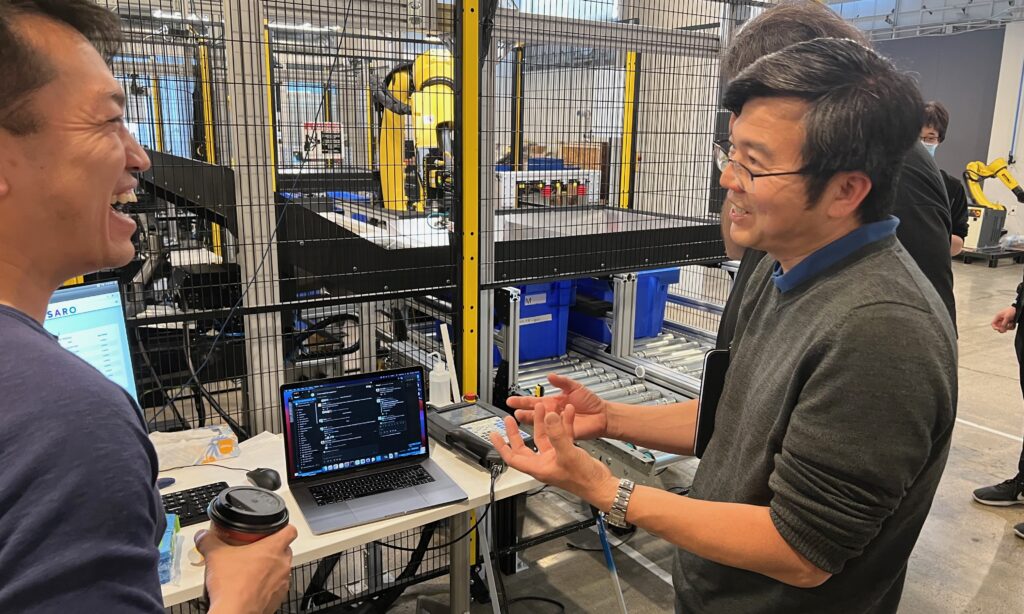