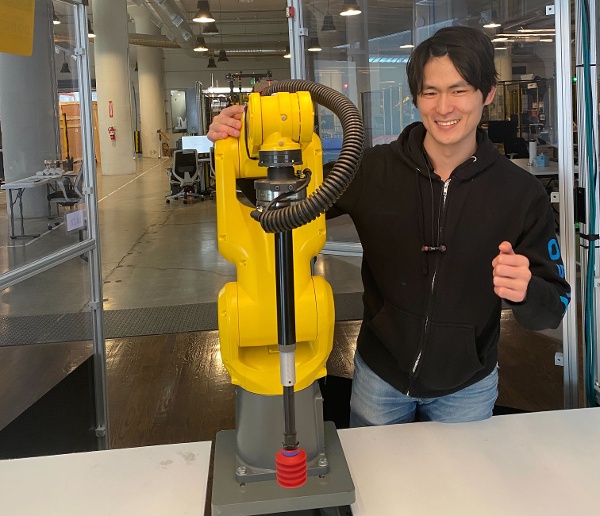
Meet our Expert
As senior director for international solutions, Kazu Komoto is one of OSARO’s experienced solutions engineers who coaches clients through the adoption of robotics for e-commerce. A problem-solver with enormous attention to both detail and strategy, Komoto has worked on deployments in the U.S., Japan, China, Singapore, Australia, and Germany. In particular, he has significant experience troubleshooting and resolving issues related to depalletization, whether it involves beverages, pharmaceuticals, grocery items, or boxed goods.
Komoto has been with OSARO for more than six and a half years. Prior to that, he worked for startups as a robotics engineer in the San Francisco area, as well as a management consulting firm where he first became involved with the robotics business. He earned his BS in Engineering Science and an MS in Mechanical Engineering from Kyoto University, focusing on human-robot interaction design. He has been a guest contributor to major publications. In 2023, he was selected as a 40 under 40 Influential Innovator in AI.
Seven ways to evaluate a depalletization system
By OSARO Staff | OSARO Ask an Expert series
Pallets are the essential and pervasive unit by which goods get organized, stacked, loaded, transported, offloaded, and then depalletized at their destination. But they can be dangerous especially when unloaded after products shift in transit. In recent years, AI-driven vision software has made industrial robots smarter – and capable of doing the heavy lifting with the precision required by depalletization (depal). Depal can improve safety, increase efficiency, reduce labor costs, and enhance product quality. Smart robots can handle different load types and sizes, as well as challenging mixed-case pallets.
Why should I shift from manual to robotic depalletization?
Komoto: There are many reasons to consider robotics in depal, but three of the top ones are:
Reduce injury
Warehouse pallets pose serious injury risks, mainly because of their weight, handling procedures, and potential for structural failure. Back and muscle injuries, which are commonplace in warehousing, account for nearly 500,000 injuries a year in the U.S. alone – at a cost of $20 billion. The U.S. Occupational Health and Safety Administration (OSHA) estimates the total economic burden of such injuries – as measured by compensation costs, lost wages, and lost productivity including ancillary costs, such as the need to pay other workers overtime to cover missing employees – is actually between $45 and $54 billion annually.
Meet crushing demand and boost efficiency
The growth in e-commerce sales has put enormous pressure on 3PLs and retail fulfillment centers to fill more orders at faster speeds. Despite inflation concerns, e-commerce sales are projected to increase 56 percent from their 2021 level of $5.2 trillion worldwide to about $8.1 trillion dollars by 2026. Robots increase throughput, require no overtime, and are flexible. They can work all night on short notice during seasonal surges.
Reduce dependence on manual labor
Another compelling incentive driving the automation of depalletization is the need to reduce reliance on manual labor in the face of a severe worker shortage that shows no signs of abating. Robots eliminate delays and costs associated with turnover, training, and surge needs. The benefits have become obvious. As a result, from 2022 to 2027, the global market for robotic depalletizers is expected to balloon by $1.7 billion to $3.5 billion.
How do I choose the right robotic depal system?
Komoto: To make an informed decision make sure you consider these 7 factors:
Operational Requirements: Assess your specific operational needs. Consider the volume of palletized goods, required throughput, and the level of automation integration desired. How will robotics fit with your warehouse workflow? How will it fit into your layout and floor space?
Load Types and Variability: Evaluate the types of loads you typically handle. Different robotic systems are designed to handle specific load characteristics, such as weight, shape, fragility, and stacking patterns. Ensure that the robotic system you choose is capable of handling your load types effectively – especially if mixed case pallets are involved.
Flexibility and Scalability: Can the system adapt to changes in product lines, packaging, and load configurations? Is it modular or mobile? Is it capable of scaling up or down based on potential future changes in your operations? How easy is it to install?
Speed and Throughput: Evaluate the robot’s cycle time, picking and placing speed, and the ability to handle multiple pallets simultaneously. Consider the reliability and uptime of the system. Downtime can impact your operations.
Safety and Reliability: Ensure that the robotic depal solution meets safety regulations. Cobots, which are smaller and move more slowly, typically work alongside workers in an open environment. However, larger, faster-moving industrial robots typically used in depal, must be fenced for safety. Look for features such as collision detection, emergency stop buttons, and protective enclosures to ensure the safety of your workers.
Integration and Compatibility: Evaluate how well the robotic depalletization system integrates with your existing infrastructure, such as conveyors, forklift, AGV/AMR, Pallet ASRS, warehouse control systems (WCS), warehouse management systems (WMS), or other automation equipment.
Support and Maintenance: Consider the technical support and maintenance services offered by potential vendors. Is there onsite deployment support? Inquire about training programs to ensure your staff is properly trained to operate and maintain the system.
Why is mixed case depal such a challenge?
Komoto: Until very recently even 3D robotic vision was not able to recognize the encased SKUs tightly packed side-by-side on a pallet, often in translucent plastic wrap such as water bottle cases. However, robotic vision, enabled by Deep Learning technology, is now able to recognize the notion of “cases” along with their dimensions and location, as a human worker would see them.
Vision has not been the only challenge with mixed cases. As the robot must handle a variety of heavy items, the end-of-arm tools, such as grippers with different vacuum cups, along with the control method, are critical. Mixed case systems may need to employ a tool changer or change pickup speed based on the item’s shape, weight or position. New depal systems utilize vision software with cameras, force torque sensors and pneumatic sensors so that the robot can make decisions about which tool and configuration to use on the fly during run time. When investigating the use of mixed-case depal, be sure your vendor has the expertise to plan and deploy all these critical assets.
How do you finance robotic depalletization?
Komoto: Evaluate the total cost of ownership by considering initial investment, maintenance costs, energy consumption, and potential productivity gains. Calculate the ROI based on labor savings, increased throughput, and improved efficiency to determine the financial viability of the solution. Ask your vendor about Robot-as-a-Service plans which shift upfront capital investment to lower and less risky annual operational costs.
It’s important to engage with multiple solution vendors, conduct site visits, and request demonstrations, as you evaluate different options before making a final decision.
OSARO is ready to help you navigate robotic depalletization for your warehouse.
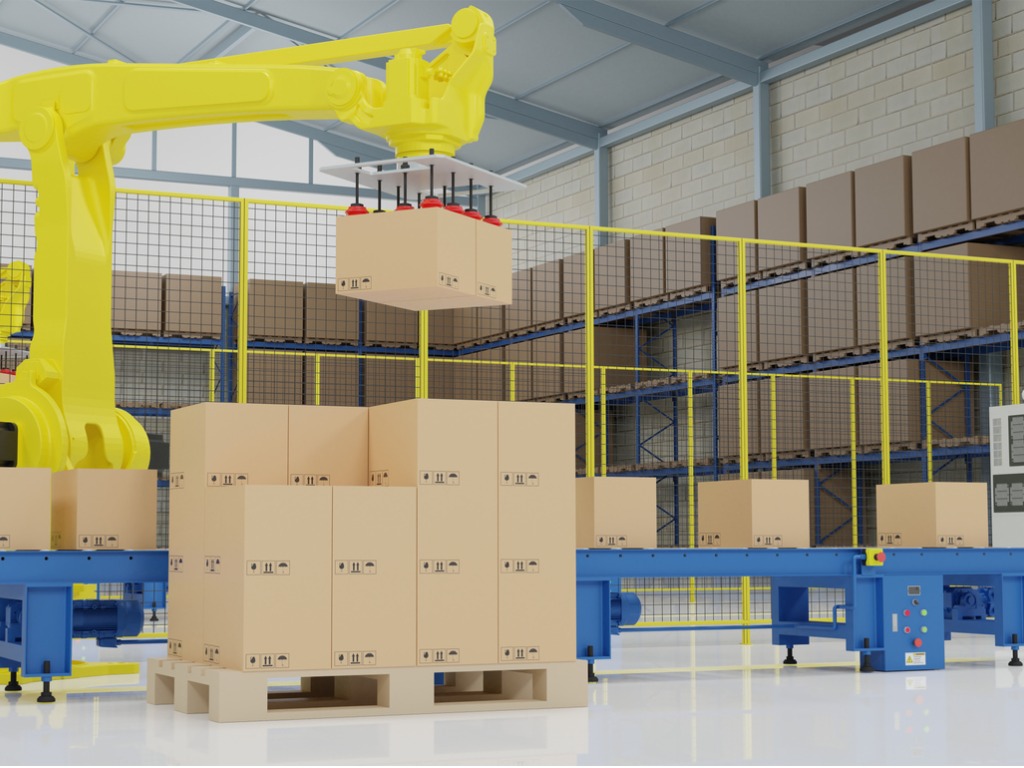