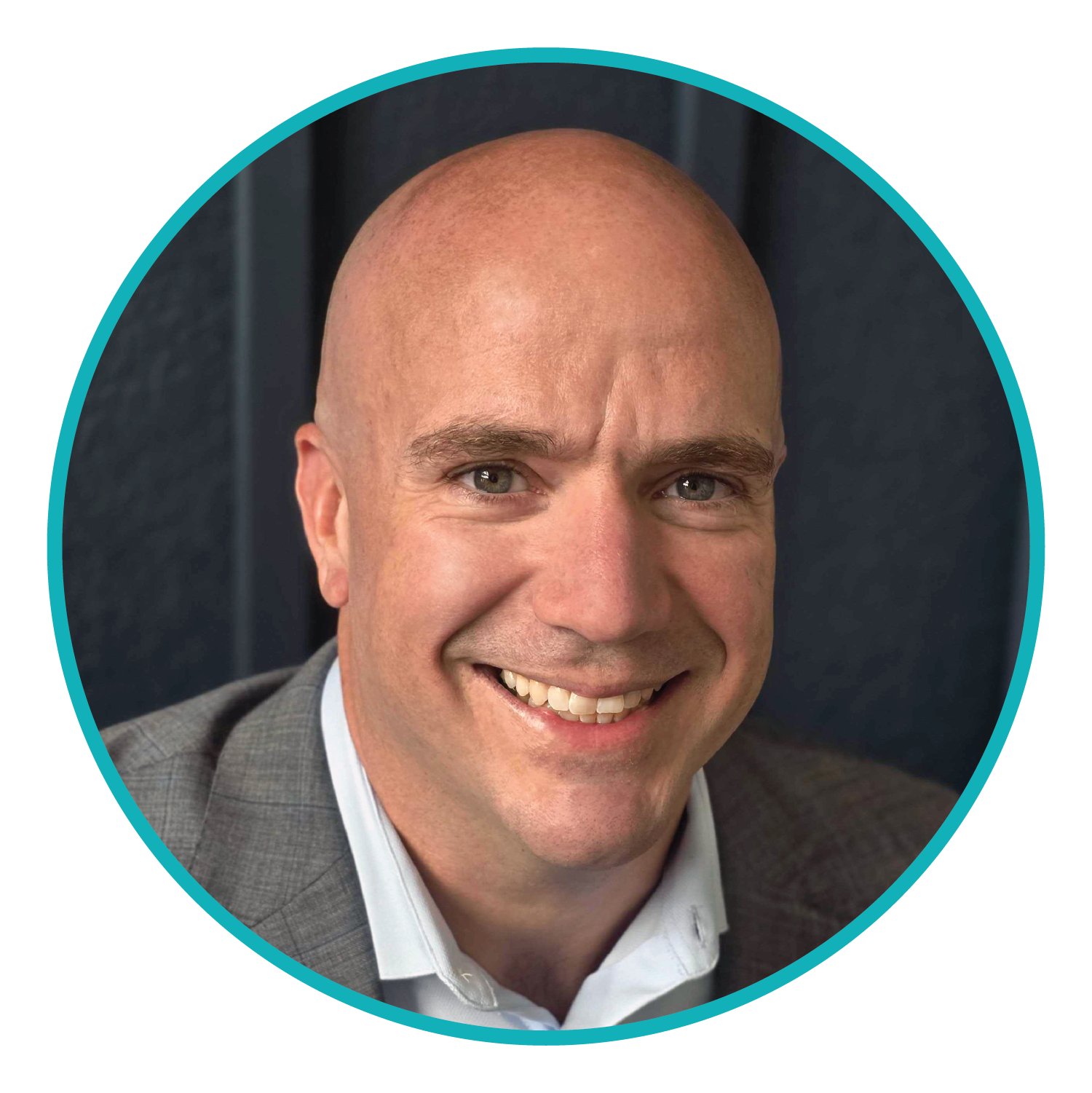
By Matt Churchill, Principal sales engineer
Matt Churchill is a Principal sales engineer at OSARO, specializing in driving innovation through practical automation design. With extensive experience in solutions architecture, project management, and application engineering, he consistently develops customer-driven solutions. His diverse background showcases his expertise in automation and mechanical design.
The promise of robotic AI
Robotics and artificial intelligence are no longer just buzzwords; they’re reshaping manufacturing, logistics, and e-commerce fulfillment. At their best, AI-enabled robots don’t just move objects from Point A to Point B — they learn from each attempt, adapt on the fly, and get measurably better over time. That’s the promise, at least.
The reality of human-tagged AI
But here’s the issue: many robotic AI deployments still rely on human supervision in one of two ways — either through human-tagged training data or remote operators intervening when a robot gets stuck. In both cases, the robot is not truly learning; it’s just outsourcing decision-making to a human and waiting for an answer.
With human-tagged data, a person reviews past performance (often just images) and labels which actions were successful. While this approach can improve accuracy over time, it requires collecting, tagging, training, and redeploying models — a cycle that can take weeks to respond to new conditions.
Remote-supervised robots, on the other hand, depend on a human-in-the-loop system where an operator steps in through an online portal to resolve failures in real time. But these interventions are made with limited information — typically just a still image with some supplementary 3D data. The operator makes a best guess and sends a command, but the system has no way to truly validate if the correction led to long-term success. Without full context from real-time sensor data, the quality of any training data harvested from these interventions is inherently flawed. Instead of the robot improving its own decision-making, it’s learning from incomplete, and often unreliable, human-provided corrections.
Both approaches create a fundamental problem — robotic decision-making remains dependent on human judgment, either before deployment (human-tagged data) or during operation (remote supervision). This makes the system slow to adapt and limits its ability to scale effectively.
Breaking free from human supervision
At OSARO, we set out to build something that doesn’t need constant supervision: AutoModel™. Our system continuously monitors its own attempts in real time, using sensor data (vision, force-torque, vacuum sensors, barcode scans — you name it) to determine if a pick or place action was truly successful. Because AutoModel automatically tags its own performance data, we can spot and address issues as they happen, retrain models in hours instead of weeks, and deploy updated behavior to the robot without human intervention. No more waiting for someone to play back the tape, guess what went wrong, and manually re-label thousands of images.
Real AI stands on its own
If your AI isn’t learning on its own, can it really be called intelligent? By eliminating the need for continuous human tagging or real-time remote supervision, AutoModel delivers on the real promise of AI — autonomous learning and adaptation. That’s how robotic systems stay ahead of changing products, workflows, and customer demands. Instead of waiting for human intervention, they get smarter with every pick.
Time to remove the training wheels
Human-in-the-loop systems can only take you so far. If you’re looking for next-level robotics that genuinely self-improve, it’s time to remove the training wheels. Let’s put the intelligence back into AI.